In the engineering world, fail-safes are important for ensuring that no harm comes to equipment, the environment, or people nearby. Fail-safes can be installed in places like airports and factories and can range from mechanisms like air brakes on railway trains and trucks to safety valves for places operating with fluids.
For students in engineering design technology, knowing how fail-safes work can be very important when helping engineers design safer structures and spaces. Specialized software, such as Autodesk Inventor, can also be a very useful tool for technicians to use for 3D mechanical design, documentation, and product simulation.
Here is what you need to know.
What Fail-safes Really Are and What They Can Do
Fail-safe devices or systems are not meant to prevent accidents or failures from occurring. Instead, they are put in place for when things do go wrong. Fail-safes are built with the expectation that failure situations will eventually happen. They prevent unsafe consequences when failure does occur. Fail-safe systems can range from mechanical and physical to electrical or electronic depending on the system or device.
For example, elevators have several sets of emergency brakes that come into effect in the event of a breakdown or power failure. Should the elevator malfunction or begin to fall, then the brakes would activate and stop the elevator from falling, or slow the fall to help keep passengers relatively safe. This would be an example of a mechanical fail-safe system.
Electronic fail-safe devices can include fuses, circuit breakers, or current limiting circuits, which interrupt electrical currents under overload conditions. As a result, they prevent damage to wiring or circuit devices.
Engineering Design Professionals Can Help Design and Test Fail-safes Before Construction
Fail-safes need to work to ensure that individuals and property are safe when using a product or working in a facility. Graduates of engineering training can turn to Autodesk Inventor and other software programs to help engineers integrate 2D and 3D data into a single environment, producing a digital representation of a prototype fail-safe device before it’s even built.
Engineering design professionals can use this technology to help design and simulate fail-safes like roller-shutter fire doors in factories, which activate and close when smoke detectors sound the alarm, even during a power outage. They can even use software programs to model and test dead man’s switches—also known as kill switches or enabling switches—on airport luggage carts and other devices, which can deactivate a product if a driver or operator becomes incapacitated, preventing injury or property damage.
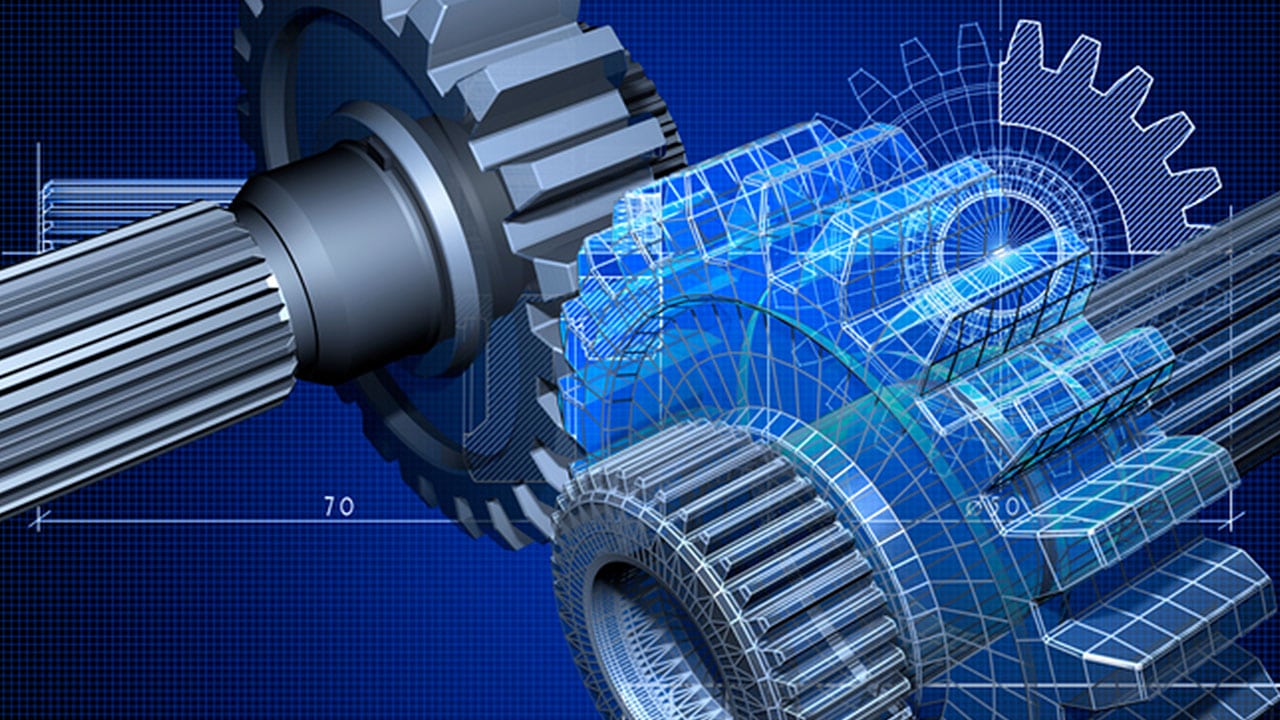
Good engineering means considering worst case scenarios and how to safeguard against them
Grads with Engineering Training Should Think “What Are Safe States”
Good engineering means considering both success and failure when designing a product or device. Safe states are what students in an engineering design technology college should have in mind when designing a system for the principle of a “fail-safe”.
What is a safe state? One way to find out is to consider the worst-case scenario if a key part of a device or system stopped functioning, and assess if the consequences of those failures are severe. At that point, those with a career in engineering design technology should engineer safeguards to prevent the worst possible outcomes. Products engineered with this question in mind can then fail in a safe and predictable manner, hence leading to a “safe state.”
Would you like a career designing a variety of different products?